Практический пример обратного проектирования, автор: Кацуя Танабики
Выемка на щитке мотоциклетного шлема сломана, а запасной части для ее починки нет в наличии. Прекрасный случай использовать современные технологии для быстрого и экономичного производства запасной части.
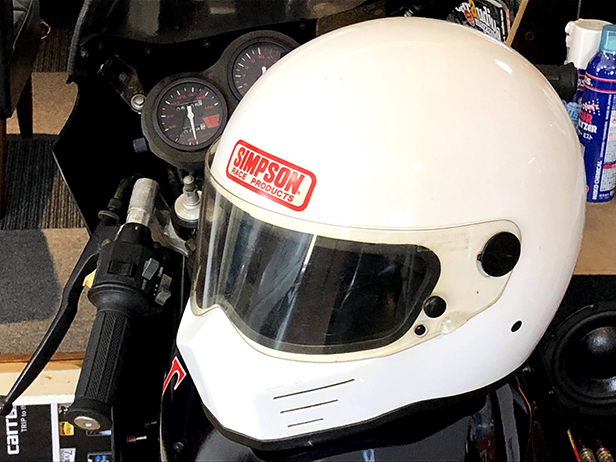
Заслонка – это небольшая пластиковая деталь, поэтому ее удобно воспроизвести с помощью 3D-принтера.
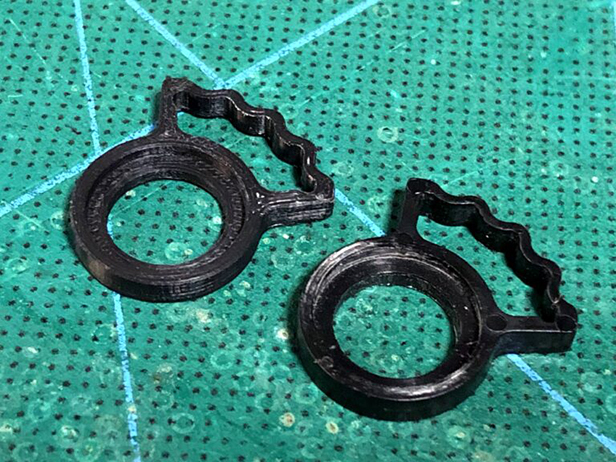
В случае со шлемом необходимы две заслонки. По одной для крепления визора с каждой стороны. Поскольку только одна заслонка сломана, оставшаяся заслонкой является ключом к проектированию и изготовлению реплики, точно соответствующей шлему, изготовленному на заказ.
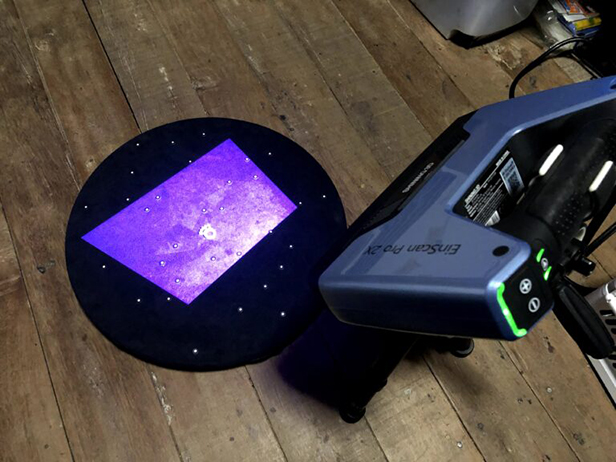
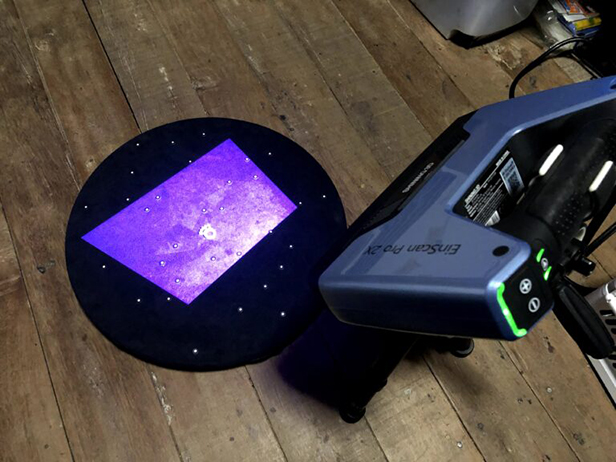
Эффективным вариантом успешного и точного сканирования объектов такого маленького размера с помощью EinScan Pro 2X является использование фиксированного режима в сочетании со штативом из дополнительного комплекта «Industrial Pack».
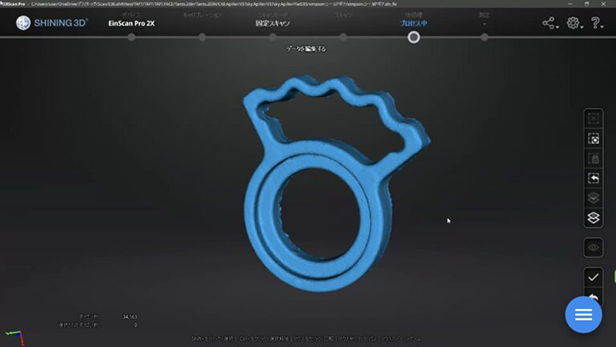
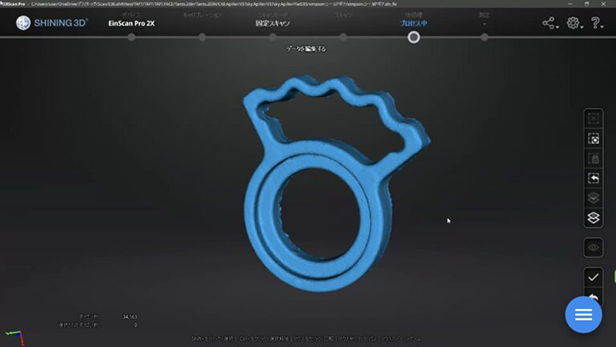
Результаты сканирования в стационарном режиме получились точными, как и ожидалось. Теперь эти данные можно использовать для «обратного проектирования» в «Fusion 360».
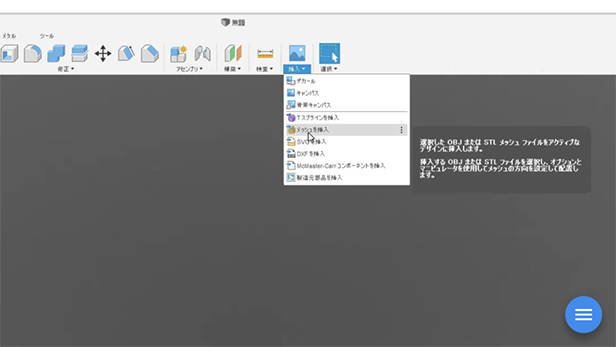
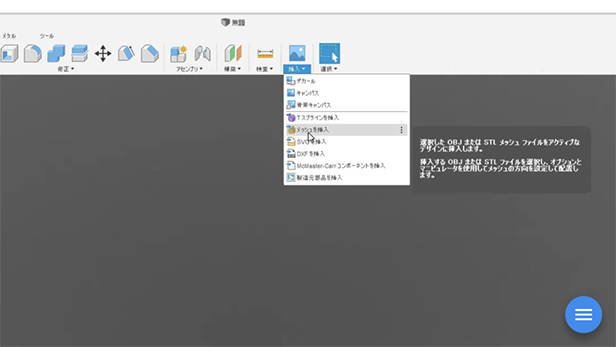
Первым шагом является импорт данных сканирования в Fusion 360 с помощью вставки сетки.
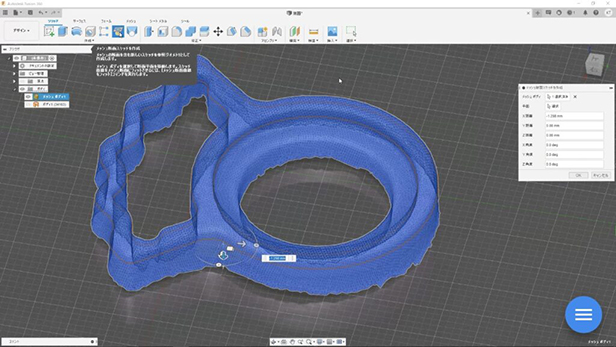
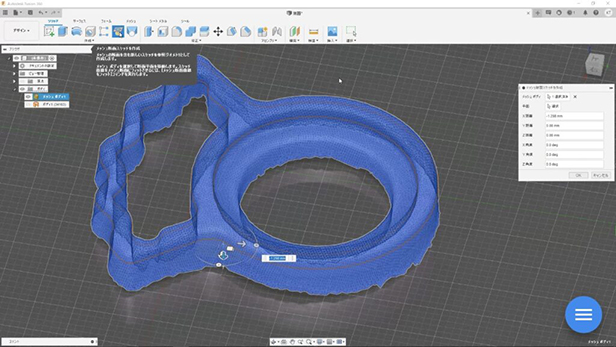
Сначала создается эскиз сечения сетки. Положение сечения настраивается на нужный уровень и подтверждается нажатием кнопки «ОК».
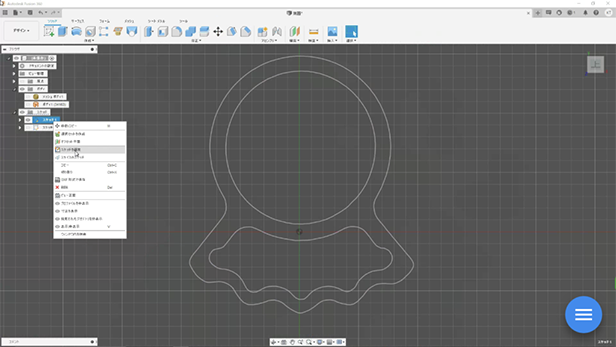
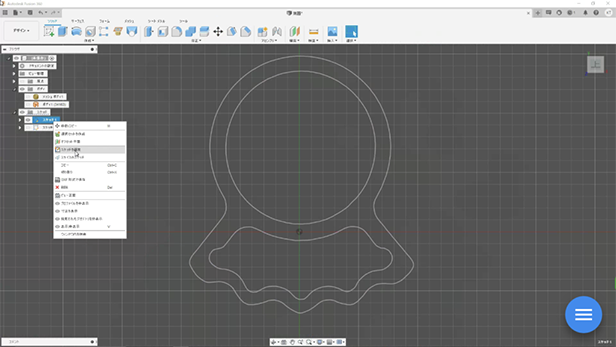
1. Щелкните правой кнопкой мыши на эскизе сечения и выберите «Редактировать эскиз» (Edit Sketch), как показано на изображении.
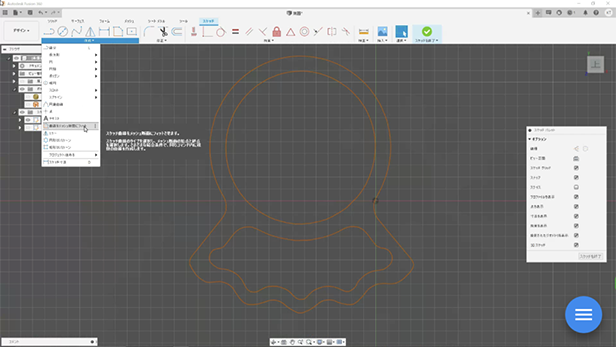
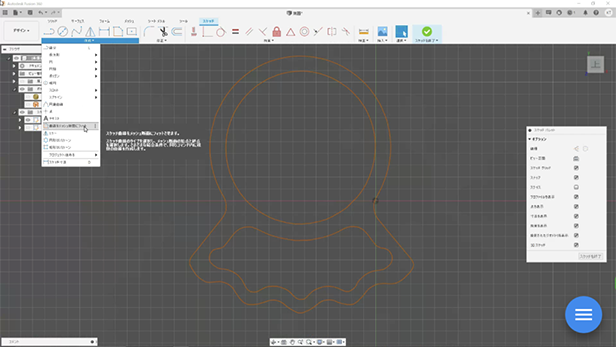
2. Выберите «Подогнать поверхность к сечению сетки» (Fit Surface to Mesh Section) в режиме «Создать эскиз» (Create Sketch).
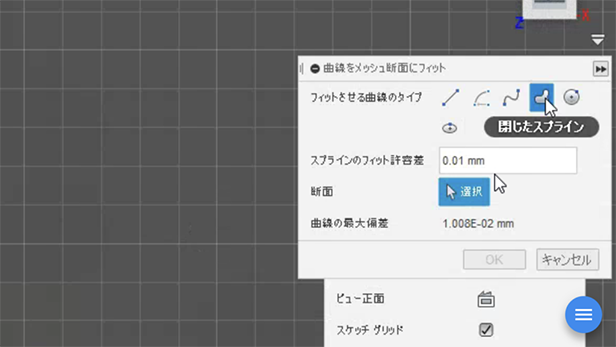
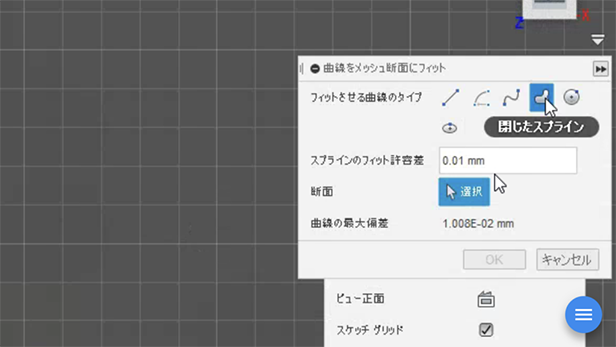
3. Выберите «Замкнутый сплайн» (Closed Spline) в качестве типа кривой для подгонки, выберите «Поперечное сечение» (Cross-section) нажмите «ОК».
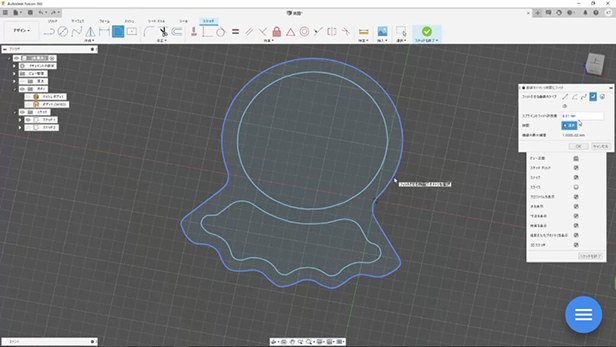
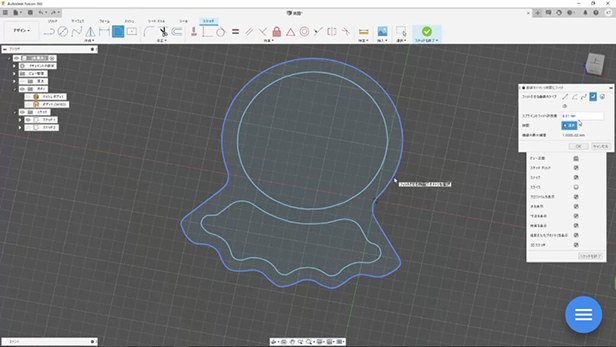
4. Хотя это не показано на рисунке, ступенчатая часть нарисована таким же образом. С помощью кривой линии эскиза, которую можно использовать для моделирования, можно завершить эскиз.
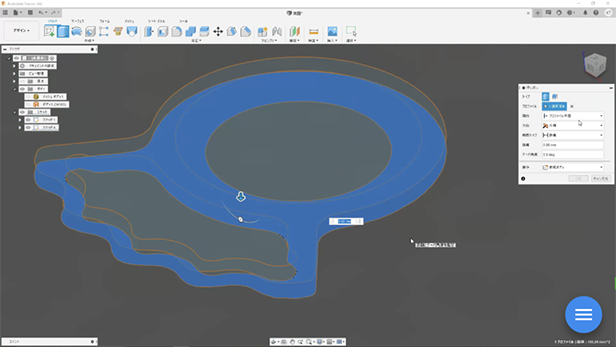
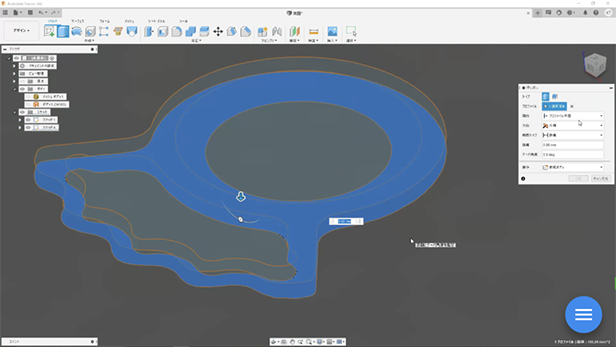
5. На вкладке «Заполненное пространство» (Solid) выберите «Выдавливание» (Extrude), после выберите поверхность для выдавливания и укажите степень выдавливания, чтобы сделать ее заполненным телом.
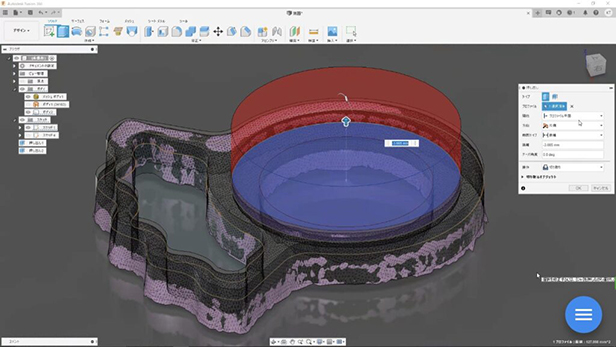
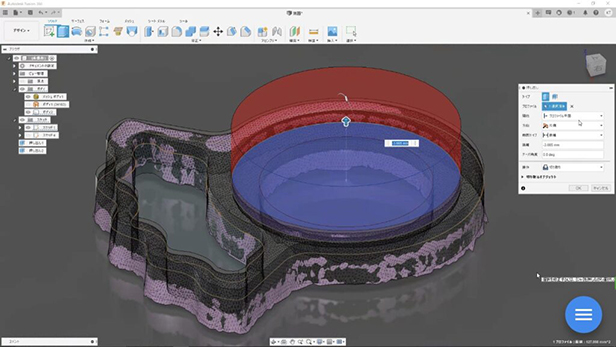
6. Аналогичным образом вырежьте деталь ступени, используя выдавливание для создания ступени.
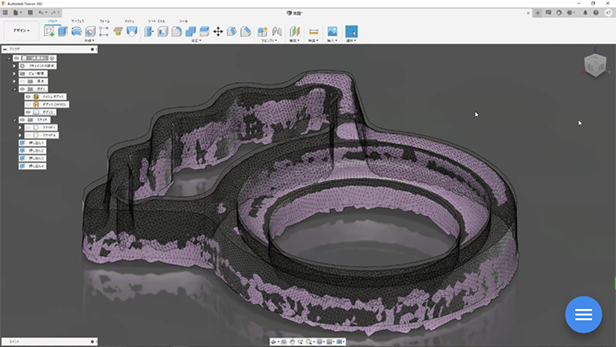
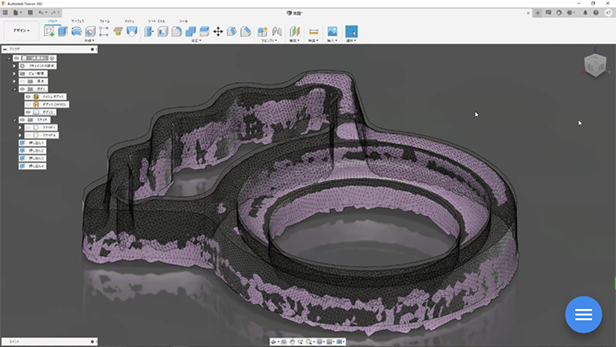
7. На последнем этапе нужно обработать деталь и удалить лишнее, а также снять фаску, чтобы придать ей ту же форму, что и у исходной детали.
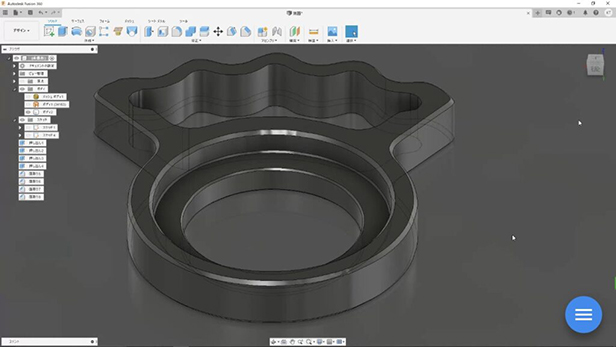
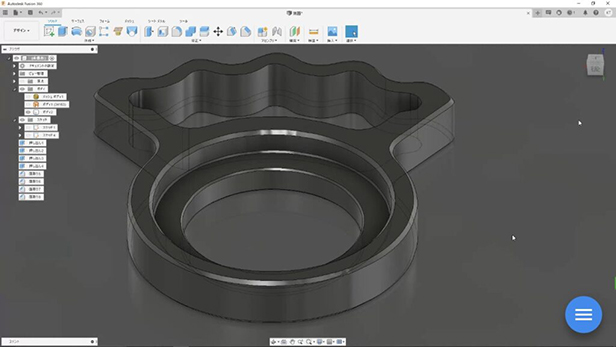
8. Модель детали завершена. Щелкнув правой кнопкой мыши по телу на вкладке, можно создать STL-файл.
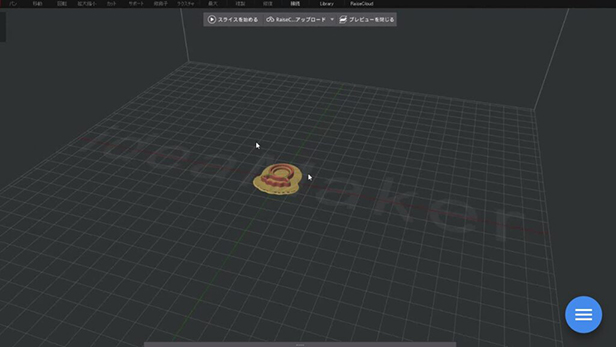
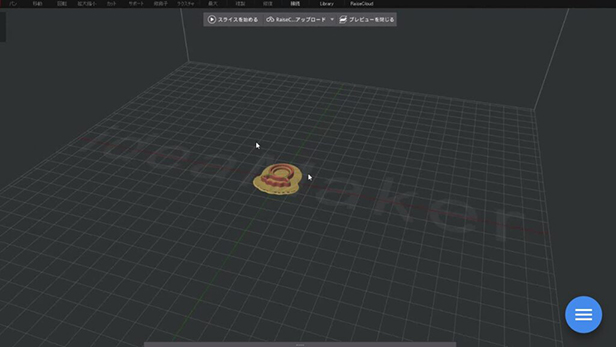
Теперь деталь готова к 3D-печати.
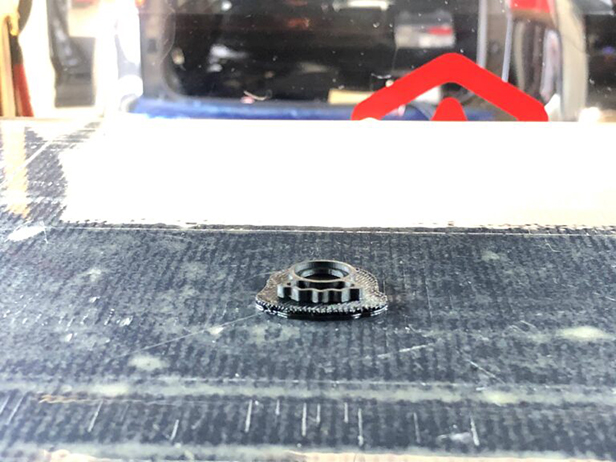
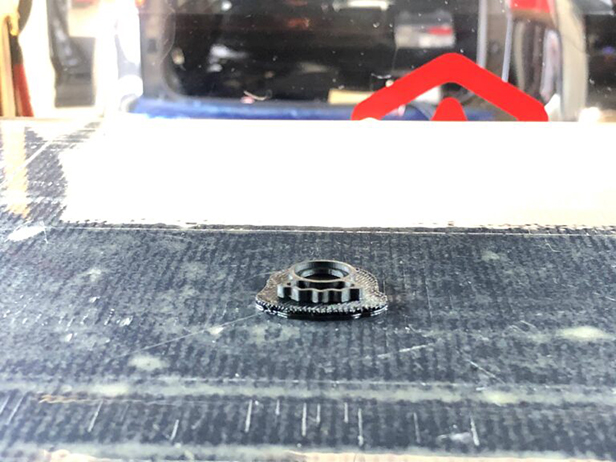
Деталь настолько мала, что процесс печати не займет много времени.
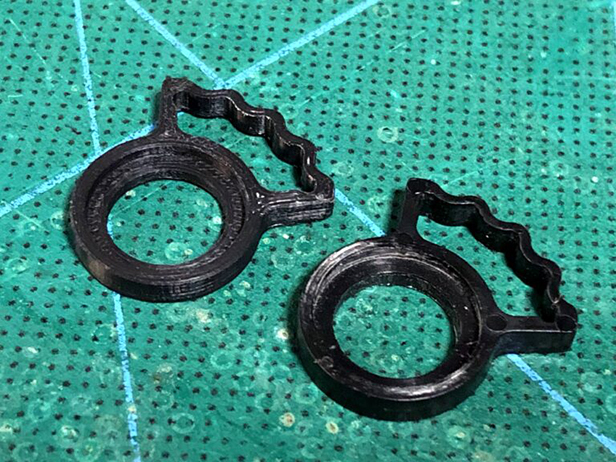
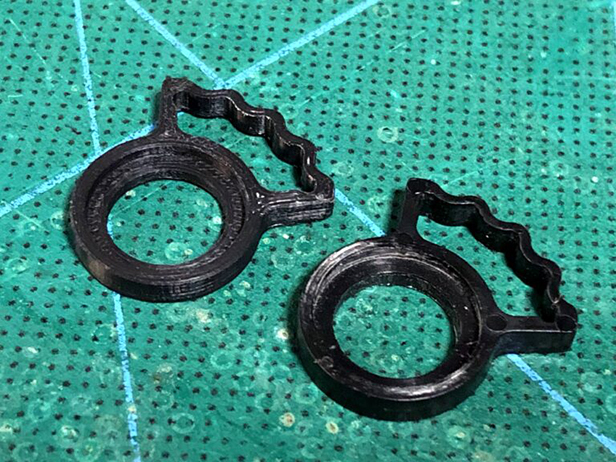
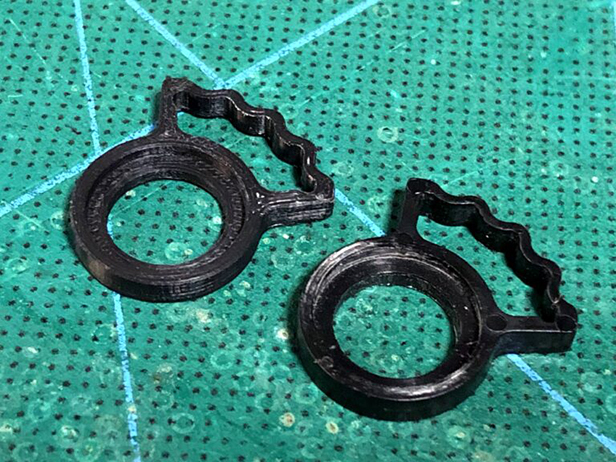
Слева – напечатанная 3D-деталь.
Включая время 3D-печати, починка шлема заняла около часа.
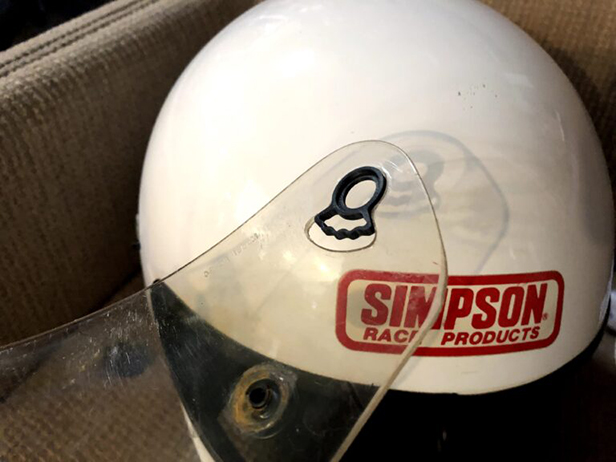
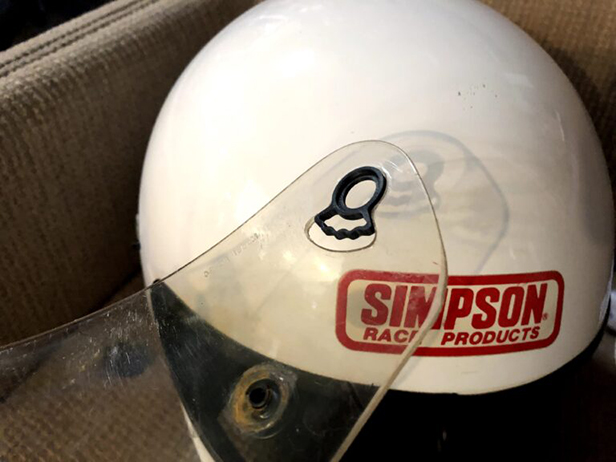
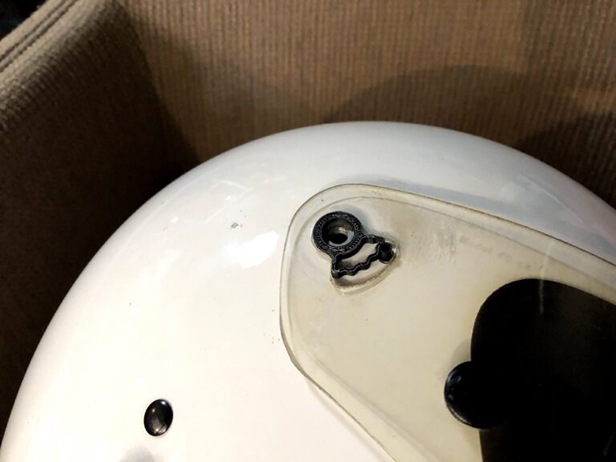
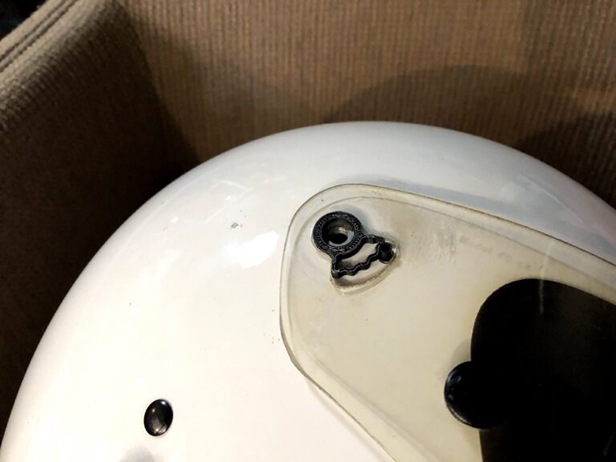
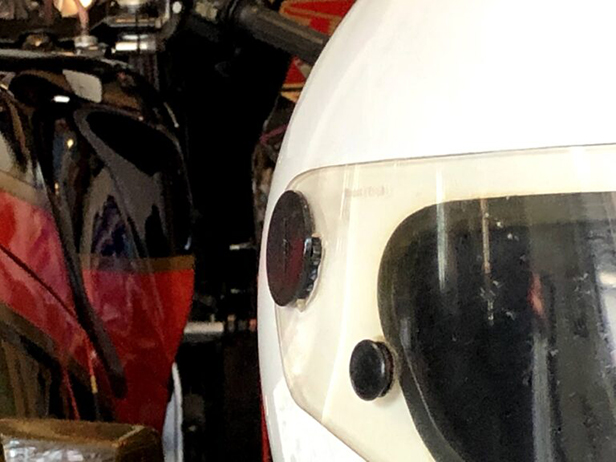
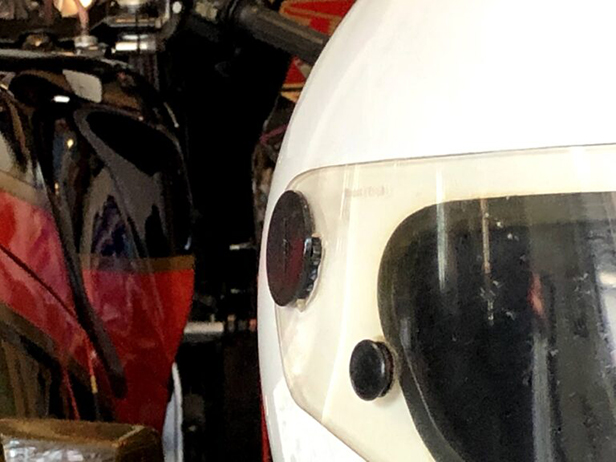
Кацуя увлекается мотоциклами и автомобилями. На своем блоге (custom-auto-maruta.com) он делится своими проектами, используя «Fusion 360» и 3D-печать в сочетании с «EinScan Pro 2X». Ему нравится сила 3D-технологии, которая позволяет ему делать все, что угодно: оригинальные детали и 3D-печатные запчасти.
Оригинальная статья на японском языке на сайте: